Controlling industrial processes is one of the more demanding scenarios for electronics — especially in extremely harsh facilities, such as heavy and military industries, electricity generation and distribution stations, and large marine vessels. These environments may expose electronics to a wide range of undesired and harmful phenomena ranging from electrostatic discharges (ESD) and contamination from wireless networks to surges and spikes in sensor and detector transmission lines.
Many of these problems can be caused by the electronic drives commonly used in industrial environments to move mechanisms. The mechanisms may either be controlled by an electronic drive directly or by traditional start/stop switching devices. In the first case, the use of electronic soft starters or variable-speed drives can introduce a significant source of harmonics and perturbances that are injected into the general AC power supply. In the second case, the use of contactors for start and stop commands can forward major spikes to the line power during switching operations. In both cases, undesired noise emissions can be coupled into the sensor signal transmission lines, introducing irregular distortions into sensor data.
These issues are typically found in industrial plants where microprocessor-based controllers must deal with inductive loads, sensors and detectors numbering into the hundreds. Processes in isolated facilities, on the other hand, suffer from other kinds of no less damaging effects. Facilities in this category include off- and onshore wind and solar farms, hydroelectric plants, atmospheric and pollution monitoring networks, water quality/quantity and flood monitoring networks, marine and fluvial hatcheries, and agricultural facilities.
In these situations, electric power lines may become a dangerous source of surges and high-voltage transients, severely damaging control devices in spite of the use of surge suppressors. Cloud-to-ground lightning and atmospheric discharges can also challenge the most robust electronic controllers and protection devices if the local electric ground installation does not match recommended minimum values. Frequently, these isolated facilities require an autonomous communication infrastructure, and aerials installed for this purpose can become an additional source of atmospheric discharges.
When controllers must be deployed in these harsh conditions, a robust electronic card interfacing the System on Module with the process becomes crucial to ensure that phenomena like those listed above do not affect sensitive electronics, like processors, memory modules and signal processing circuits. Additionally, an interface board is required to adjust the electric values used by industrial field sensors and actuators to the ranges used by the internal electronics. The most commonly used ranges of electric signals worldwide are summarized below.
- Detectors to be connected to processor GPIOs as digital inputs: dry contact returning power supply positive (usually 12 or 24 V DC) or negative pole (0 V).
- Drives, actuators, contactors, solenoids to be connected to processor GPIOs as digital outputs: dry contact or active 12 or 24 V DC, supplying the required switch-on current.
- Sensors to be connected to processor ADCs as analog inputs: “current loop” 4 to 20 mA, active or passive; 0 to 10 V DC.
- Variable-speed drives and setpoint-commanded controllers to be connected to processor DACs as analog outputs: same ranges as in previous points.
Therefore, a robust and lasting interface is the only way to ensure the reliability of the whole embedded control system.
In response to this challenge, ISURKI has developed the so-called TESDA board, an industrial-grade digital and analog input/output board for the Colibri and Apalis families of System on Module devices from Toradex. ISURKI’s TESDA hybrid input/output board allows Colibri and Apalis SoMs to interface with devices in the field, such as sensors, detectors, actuators and drives. It has been designed to be suitable for deployment in harsh industrial environments.
The TESDA board features 1.4 kV opto-isolation in all inputs, offering robust protection against challenging electrical conditions (e.g., over-voltages, surges, interference), including a 12 V DC auxiliary supply for detectors and sensors. All digital inputs and outputs are equipped with LED indicators. Version 1.2 of the board additionally includes 2 A solid-state relays for unlimited operating life.
The TESDA board directly interfaces with Toradex Iris and Ixora carrier boards through their 40-pin extension connector, and it offers a mechanical holder for the Iris carrier board — essentially acting as a carrier board itself. Since its supply is directly forwarded from the carrier board, no other connections or cables are required.
Further technical specifications for this board include:
- 4 digital inputs, for voltage-free (dry) contacts or passive detectors (i.e., proximity inductive detectors) with included 12 V DC auxiliary supply
- 4 pin-to-pin configurable digital inputs/outputs. Digital outputs are solid-state relays with 1 SPDT contact and 2 A switching power
- 4 x 4–20 mA (current loop) analogue inputs, individually configurable as active or passive signals, including 12 V DC auxiliary supply
- Interface with CPU: 2 × 20-pin headers (–X1), 100% compatible with System on Module (SoM) central boards from Toradex’s Colibri and Apalis families
- Input/output connectivity: independent 12-pin detachable Wago aerial connectors (included)
- LEDs: 12 V DC auxiliary power supply, DIs and Dos
On-the-Shelf Toradex- and TESDA-based Industrial Computer
ISURKI also offers a DIN rail-mounted plug-and-play housing for a complete set consisting of a SoM, an Iris carrier board, and a TESDA board, all housed in the so-called IRIS BOX PC (see illustration).
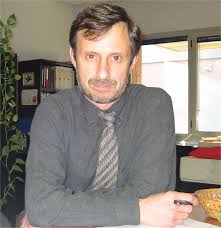
The post Interfacing Toradex Boards for Process Control in Severe Environments appeared first on ELE Times.
No comments:
Post a Comment